Introduction
In the olden times there was the concept of "Zero Defect" but it was considered more as a hypothetical term rather than having a more practical aspect because though the companies propagated that their processes or services were of Zero Defect but very few customers relied on them because defects were always there. A "Defect" can be defined as any product or service that does not conform to the set standards or satisfaction of the customer. Now, Six Sigma is a concept that tries to achieve a near zero defect with 3.4 defects in a million events.
What is Six Sigma?
Six Sigma is a methodology used to improve any business process by constantly reviewing, updating and re-tuning the existing process. Six Sigma provides the tools to improve the capability of any business process. Six Sigma professionals evaluate a business process and determine ways to improve upon the existing process. Six Sigma incorporates the same principles and techniques used in Business, Statistics, and Engineering.
Six Sigma improves the process performance, decreases variation and maintains consistent quality of the process output. This leads to defect reduction and improvement in profits, employee morale, product quality and finally customer satisfaction.
Six Sigma Strives for perfection every time. It allows for only 3.4 defects per million opportunities for each product or service transaction.
Six Sigma relies heavily on statistical techniques to reduce defects and measure quality.
Evolution of Six Sigma
Six Sigma was originally centered around manufacturing improvements. The reason for this was knowledge of the statistical tools in the manufacturing functions and the ease with which we can quantify the benefits. However the customers did not readily see these improvements. The approach was therefore broadened to all business operations. The success of these companies with the six sigma approach caught the attention of the Wall Street making it a popular strategy that is being adopted by many organizations worldwide. Indian organizations such as Wipro, Tata Motors, Hero Motors, Godrej-GE have also adopted six sigma strategy to improve their businesses (Reference: Business Today,
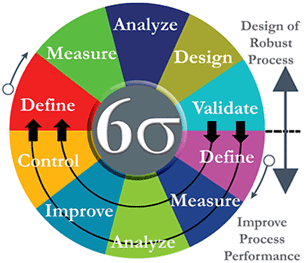
1 comment:
wr z info on motorola... benchmarking...this is critical for how six sigma came about!!
Post a Comment